Manhattan Supplier Quality Control: Tips for Excellence
In today's competitive business landscape, ensuring quality control from suppliers is crucial for your success. As a business owner or manager, you know that the quality of your products directly impacts customer satisfaction and your bottom line. Quality assurance isn't just a buzzword; it's a vital part of your supplier quality management process that can make or break your reputation in the market.
You'll find that implementing effective quality control procedures and a robust quality management system can lead to significant improvements in product quality and overall business performance. This article will guide you through establishing clear quality standards, using supplier scorecards, conducting rigorous audits, and leveraging technology to enhance your supplier quality assurance. By following these supply chain quality management best practices, you'll be better equipped to maintain high standards and stay ahead in the competitive Manhattan market.
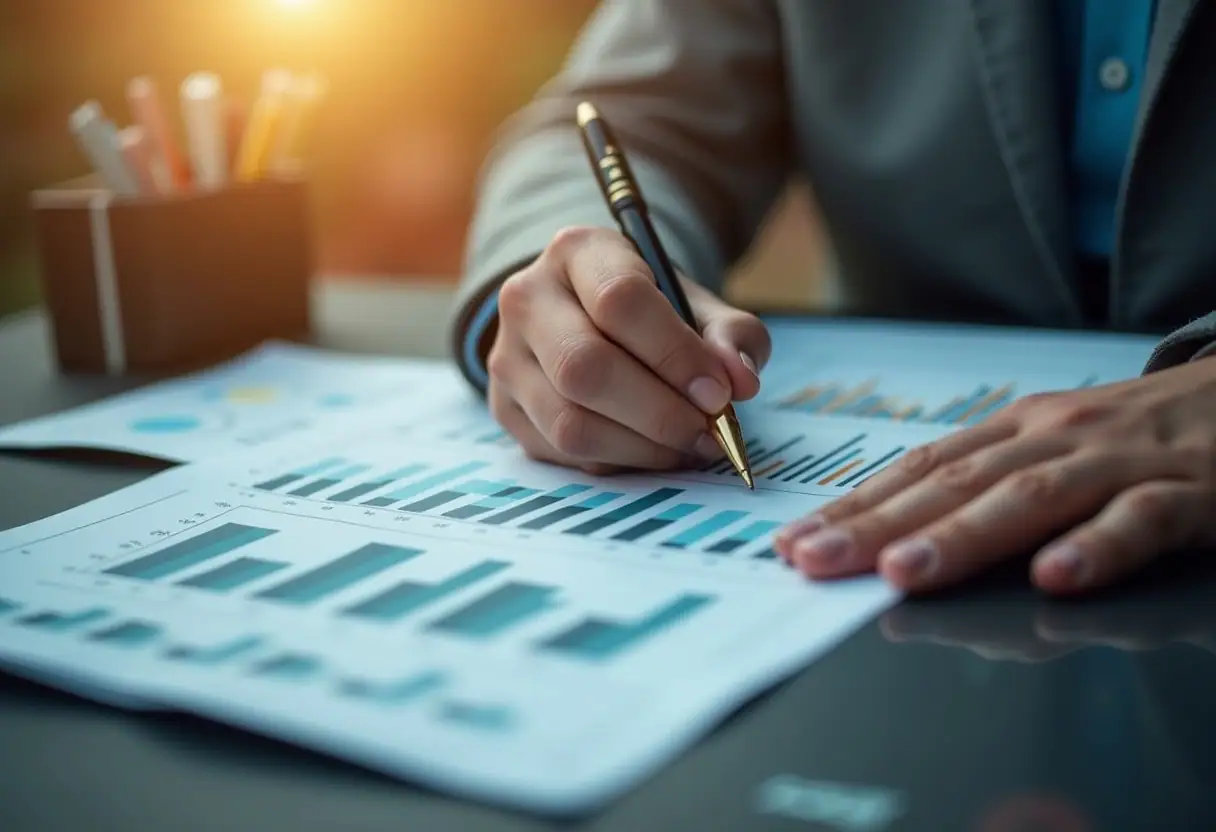
Establishing Clear Quality Standards
To ensure excellence in supplier quality control, you need to establish clear performance criteria. This process involves defining measurable criteria, effectively communicating these standards to your suppliers, and regularly reviewing and updating them.
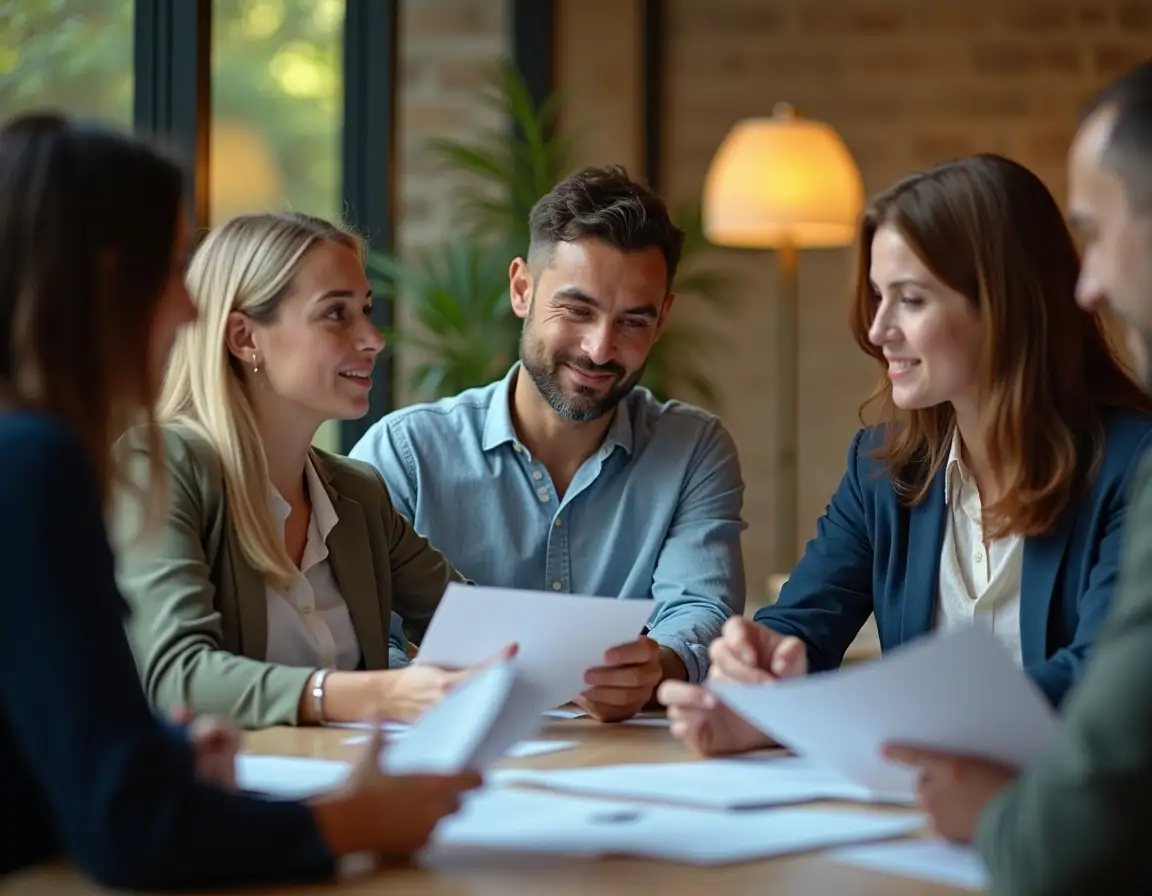
Defining measurable criteria
Start by clearly outlining the quality standards and specifications for products or services. This step is crucial for effective supplier quality management (SQM), which is the process of monitoring a supplier's ability to meet your needs. Define quality criteria that are specific, measurable, and aligned with your business requirements. For instance, an electronic components manufacturer may set minimum acceptable performance levels for each component, such as PPM (parts per million) defect rates or CSL (customer satisfaction level) targets.
Communicating standards to suppliers
Once you've defined your quality criteria, it's essential to communicate your expectations clearly and consistently to your suppliers. This communication helps to avoid misunderstandings, errors, and disputes that can affect your product quality performance, customer satisfaction, and reputation. Ensure that your suppliers understand the quality criteria and performance metrics, such as PPAP (Production Part Approval Process) or APQP (Advanced Product Quality Planning) requirements. Consider using written agreements or contracts to provide a reference point for future discussions.
Regular review and updates
Supplier quality management is an ongoing process that continues through the entire life cycle of a product and for the duration of your relationship with a particular supplier. Regularly evaluate supplier performance using a supplier rating system to maintain high standards and ensure accountability. Conduct periodic reviews to assess your supplier's adherence to contract standards, delivery times, and overall quality. Provide constructive feedback based on objective metrics and key performance indicators (KPIs). Keep your suppliers updated on any changes in requirements or expectations.
By implementing these practices, you'll be better equipped to maintain high-quality standards in your supply chain management. For a free consultation and quote on your next high-end renovation project, contact KS Renovation Group.
Implementing a Robust Supplier Scorecard System
To enhance your supplier quality control, implementing a robust supplier scorecard system is crucial. This tool, also known as a supplier report card, allows you to objectively evaluate and monitor your vendors' performance, helping you make informed decisions about your supplier selection and supplier collaboration.
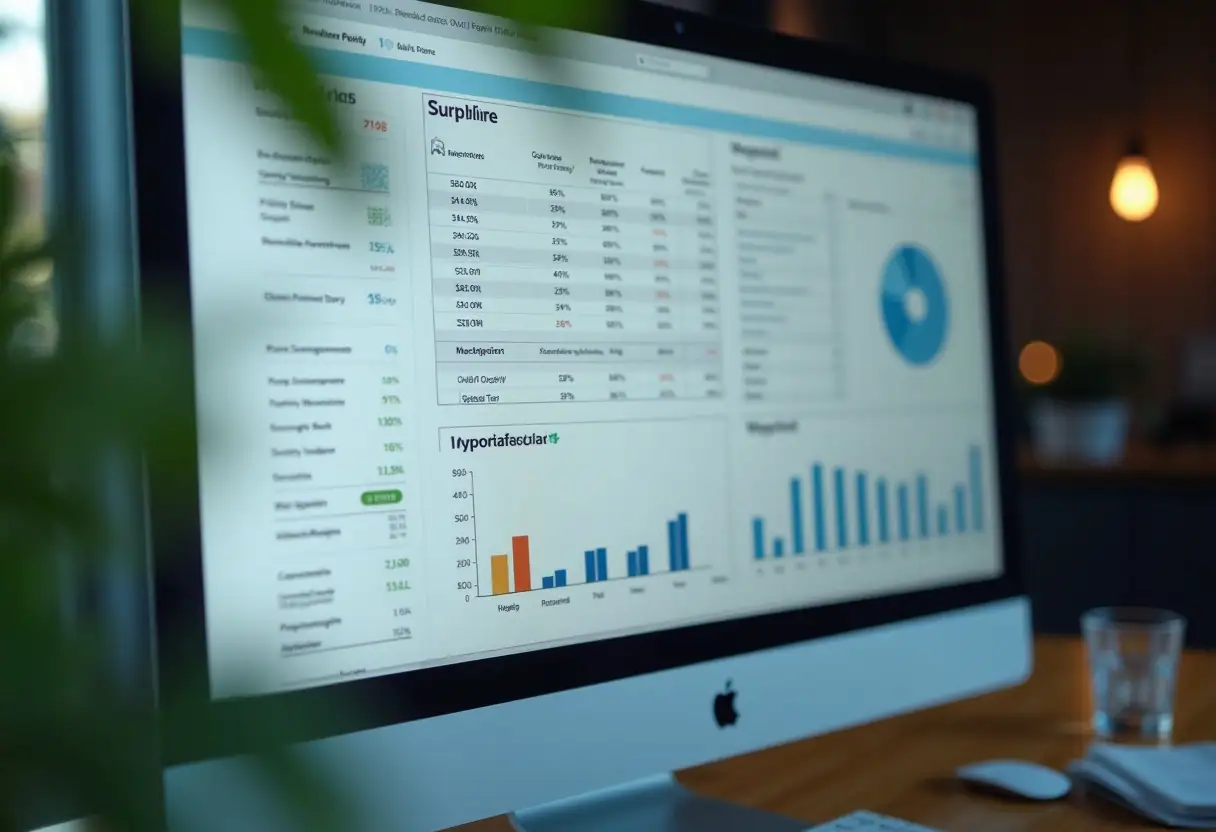
Key Performance Indicators (KPIs)
Start by identifying the most important KPIs for your business. Focus on 2-3 key metrics to get a well-rounded view of your suppliers' performance. Common KPIs include:
- On-time delivery
- Product quality
- Cost control
- Customer service
- Responsiveness
These supplier scorecard metrics should align with your company's specific objectives and be clearly defined in advance. Consider using a supplier scorecard template or supplier evaluation scorecard to standardize your assessment process.
Regular Performance Reviews
Set up a consistent schedule for performance measurement. For top-tier suppliers, monthly or quarterly check-ins are recommended. During these reviews:
- Assess supplier adherence to contract standards
- Evaluate delivery times and overall quality
- Provide constructive feedback based on objective metrics
Consider using a centralized portal or supplier evaluation tool to streamline this process. A supplier performance scorecard or vendor scorecard can provide valuable data-driven insights for your vendor management strategy.
Continuous Improvement Plans
Use the data from your supplier KPI scorecard or vendor report card to develop actionable improvement plans:
- Identify areas where suppliers are underperforming
- Work collaboratively with vendors to address issues
- Set clear targets for improvement, such as iatf target or acceptable ppm for manufacturing
- Regularly track progress towards these goals
Remember, supplier performance metrics scorecard is an ongoing process that should lead to continuous improvement in your supply chain .
For a free consultation and quote on your next high-end renovation project, contact KS Renovation Group.
Implementing Rigorous Supplier Audits
Implementing rigorous supplier audits is crucial to ensure quality control and compliance with your standards. Supplier audits provide an objective evaluation of supplier processes and compliance with regulatory requirements. These audits are essential for identifying potential issues related to purchased products or services that could impact your internal production.
On-site inspections
On-site inspections are a critical component of supplier audits. Before starting, clearly define your objectives, especially when auditing a new supplier. Develop a comprehensive supplier audit checklist that includes key areas such as product design processes, purchasing practices, quality management practices, and risk assessment strategies. Schedule a convenient date with the supplier for the audit and conduct thorough on-site evaluations.
Documentation reviews
During the audit process, focus on reviewing supplier quality documentation and records. These are essential for ensuring that your suppliers meet your quality rating system and expectations, as well as for complying with regulations. Documentation reviews help you monitor and improve supplier performance, identify and resolve issues, and support continuous improvement initiatives.
Corrective action plans
If issues are identified during the audit, implement corrective action plans (CAPs). An effective CAP identifies the root cause of problems and prevents their recurrence with rigorous documentation. Develop SMART (specific, measurable, achievable, realistic, and time-bound) goals and allocate feasible deadlines for addressing identified issues. Regularly follow up to ensure the CAP has resolved the problem and continue documenting lessons learned for future reference.
For a free consultation and quote on your next high-end renovation project, contact KS Renovation Group.
Implementing Effective Supplier Training Programs
Quality control best practices
To ensure excellence in supplier quality control, you need to implement effective training programs. Start by establishing a work environment that upholds quality standards and ensures safety protocols. Focus on process standardization by defining procedures and training personnel to follow them appropriately. Implement in-process inspections and First Article Inspections (FAI) to catch issues early. Use data-driven goals and statistical process control to drive continuous improvement and detect variations. Encourage innovation and supplier responsiveness through training initiatives.

Regulatory compliance training
Compliance training is fundamental to your company's success. It enhances employee and public safety, fosters awareness of prescribed procedures, and empowers employees to act with integrity. Implement compliance training programs to educate employees about relevant industry regulations and their specific organizational roles. This training yields financial benefits by averting non-compliance costs and boosting profitability. Ensure suppliers understand key requirements like PIQ (Product Information Questionnaire) and other regulatory standards.
Continuous education initiatives
Implement continuous improvement initiatives to enhance organizational processes and foster resilience. Regularly evaluate and refine processes to identify inefficiencies and implement changes promptly. Integrate advanced analytics and reporting tools to enhance data visibility and enable more informed decision-making. Foster a culture that embraces change by involving employees in the improvement process.
For a free consultation and quote on your next high-end renovation project, contact KS Renovation Group.
Leveraging Technology for Quality Control
Real-time monitoring systems are essential for maintaining high standards of product quality. By implementing quality control software with real-time alerts, you can detect and address issues as they occur, saving time and reducing waste. For instance, Teradyne implemented a real-time supplier quality system that allowed them to capture critical parametric performance metrics automatically before products shipped out.
Data analytics for performance insights can significantly enhance your supply chain planning and forecasting. By analyzing vast data sets, you can make informed decisions leading to a more efficient supply chain. Teradyne used Western Electric Rules and Statistical Process Control analytics on source data to identify emerging trends and take corrective actions before potentially bad components were shipped.
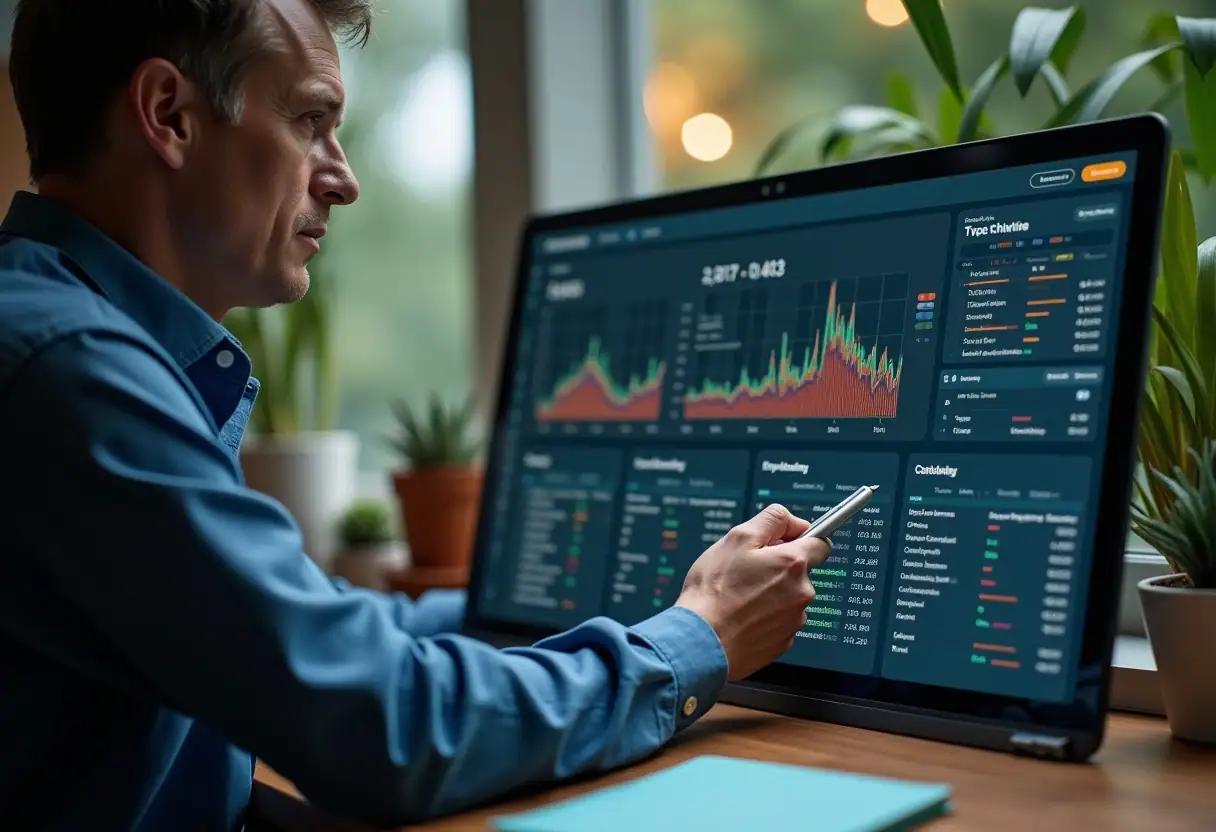
Automated inspection tools can streamline your quality control processes. For example, AssurX Supplier Quality Management software automates the quality management of suppliers, contract manufacturers, and service providers. It enables controlled, consistent, and timely management of supplier quality, helping you respond to supply chain issues faster.
For a free consultation and quote on your next high-end renovation project, contact KS Renovation Group.
Conclusion
Ensuring top-notch supplier quality control is crucial to staying ahead in Manhattan's competitive business landscape. By setting clear standards, implementing robust scorecards, conducting thorough audits, providing effective training, and leveraging cutting-edge technology, you can significantly boost your product quality and overall business performance. These strategies have a strong influence on customer satisfaction and your bottom line, making them essential for long-term success.
To put these practices into action, it's vital to foster a culture of continuous improvement and open communication with your suppliers. Regular performance reviews and data-driven decision-making are key to maintaining high standards and addressing issues promptly. For those looking to elevate their renovation projects, KS Renovation Group offers free consultations and quotes for high-end renovations, helping you bring your vision to life with quality assurance at every step.
FAQs
1. What are the best practices for managing supplier quality?
To effectively manage supplier quality, it is essential to establish performance requirements for your suppliers. You should define and document quality requirements clearly, perform both initial and ongoing qualifications of suppliers, and manage corrective and preventive actions processes diligently.
2. How can supplier quality issues be resolved?
To address quality issues with suppliers, start by identifying and clearly communicating the issue. Next, investigate to find the root cause and implement a corrective action. Monitor the effectiveness of this action and evaluate the supplier's performance improvement. Additionally, focus on preventing future issues and sharing best practices across the board.
3. How do you ensure that quality control measures are effectively implemented and maintained?
Quality control measures can be maintained by conducting regular inspections and providing thorough training to staff. Establish clear quality standards, actively seek feedback, and act on it. Continuously optimize processes based on performance data and regularly reassess and adapt your quality control strategies to meet new challenges and maintain high standards.
4. What skills are important for a successful supplier quality engineer?
A supplier quality engineer should develop several key skills to excel in their role. These include proficiency in Eight Disciplines Problem Solving (8D), auditing, quality management, statistical process controls, and root cause analysis. These skills are highly valued and can significantly enhance a professional's effectiveness in the field.
KS Renovation Blog
Get Inspired
Meaningful information about home remodeling for the true NYC homeowners.