Top 7 Construction Materials and Tech Trends in Manhattan for 2024
As Manhattan's skyline continues to evolve, the construction industry is gearing up for exciting changes in 2024. You're about to discover the latest construction materials trends 2024 that are reshaping the Big Apple's building landscape. From eco-friendly building practices to cutting-edge green construction technologies, these innovations are set to transform how we build and live in one of the world's most iconic cities.
Get ready to explore a world where sustainable building materials meet smart technology integration. You'll learn about modular construction methods that are speeding up project timelines and how 3D printing is revolutionizing the way we create structures.
These construction industry trends are not just shaping the future of construction – they're creating a more efficient, sustainable, and technologically advanced Manhattan for tomorrow.
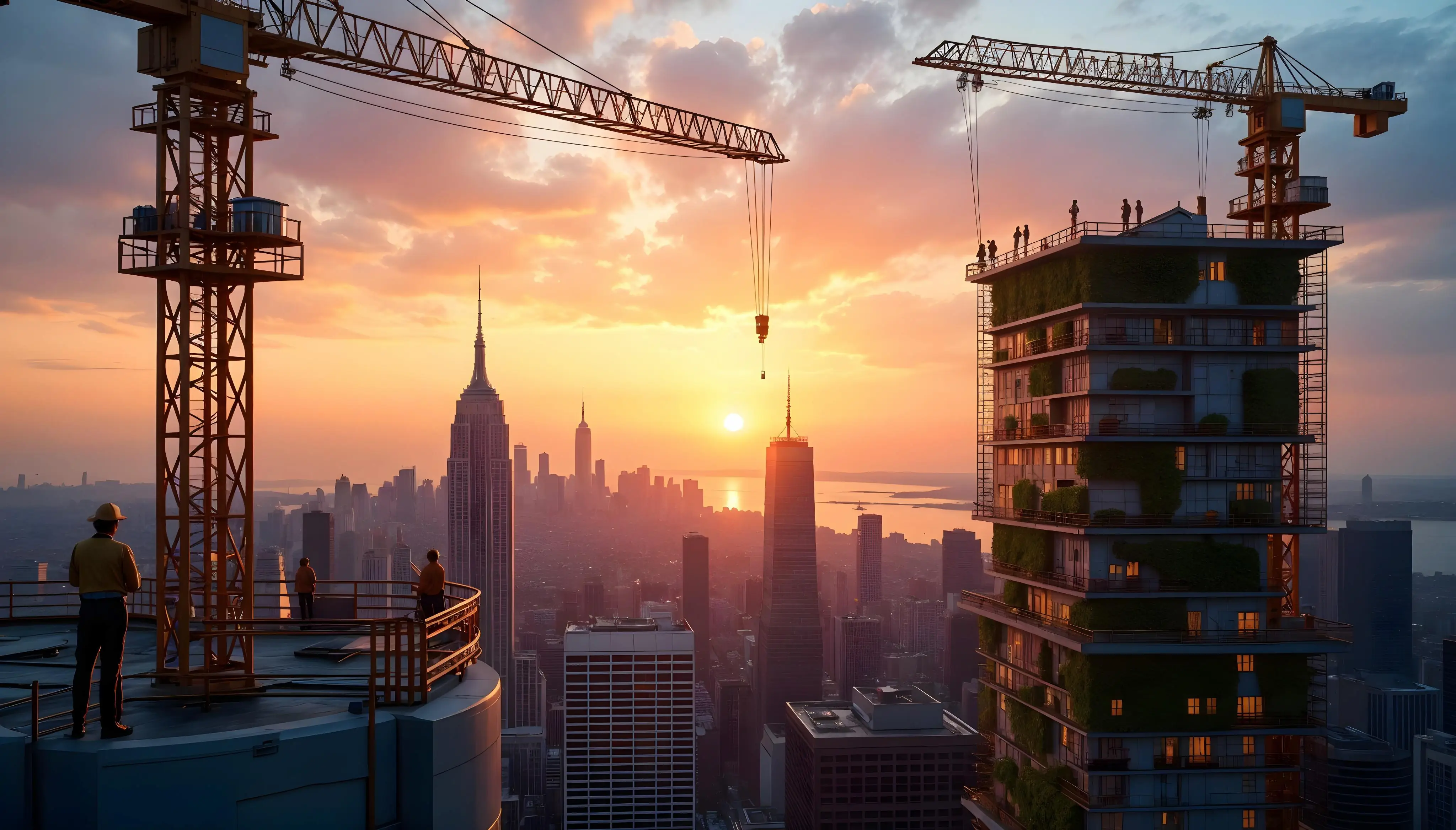
Sustainable Building Materials Taking Center Stage
As construction materials trends 2024 continue to evolve, sustainable building materials are taking center stage in Manhattan's construction industry. With a growing focus on eco-friendly building practices, builders and developers are embracing innovative sustainable building materials to reduce their environmental impact and create more sustainable structures.
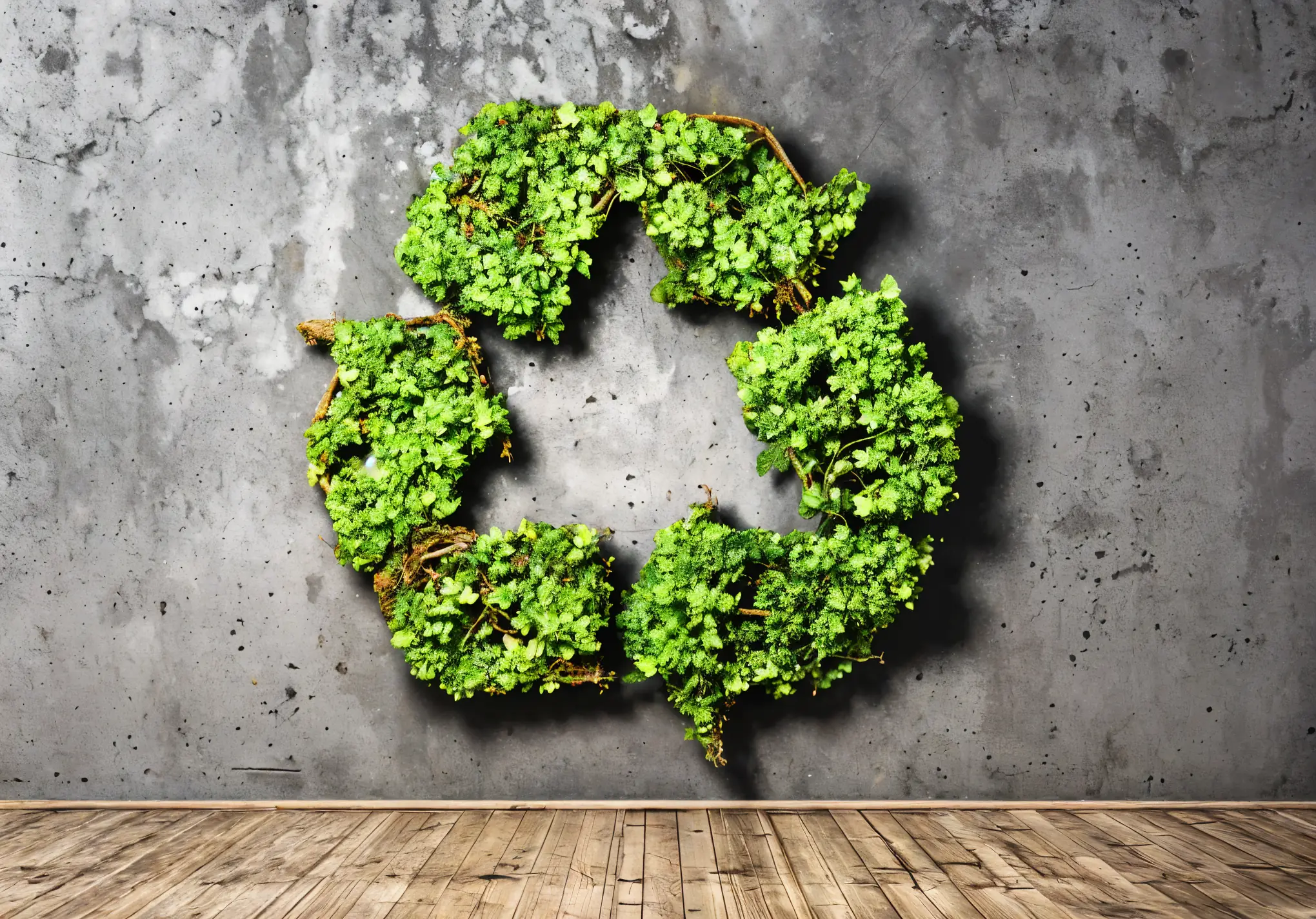
Green concrete and its applications
One of the most significant advancements in environmentally friendly construction is the development of green concrete. This eco-friendly concrete alternative to traditional concrete has a lower carbon footprint and offers improved performance. In New York City, the adoption of sustainable concrete solutions has gained momentum, with several initiatives aimed at improving concrete sustainability in construction.
The city has introduced a "Buy Clean Concrete" regulation, set to take effect in 2025. This measure will impose limits on emissions from concrete used in public construction and transportation projects funded by the state. By implementing these regulations, New York aims to achieve carbon neutrality at the economic level by 2050.
Sustainable concrete alternatives offer numerous benefits, including reduced greenhouse gas emissions, improved stormwater management, and increased durability. For example, pervious concrete allows rainwater to pass through, replenishing groundwater and reducing runoff. High-performance concrete mixes are designed for increased durability, reducing the need for frequent repairs and replacements.
Recycled steel and its benefits
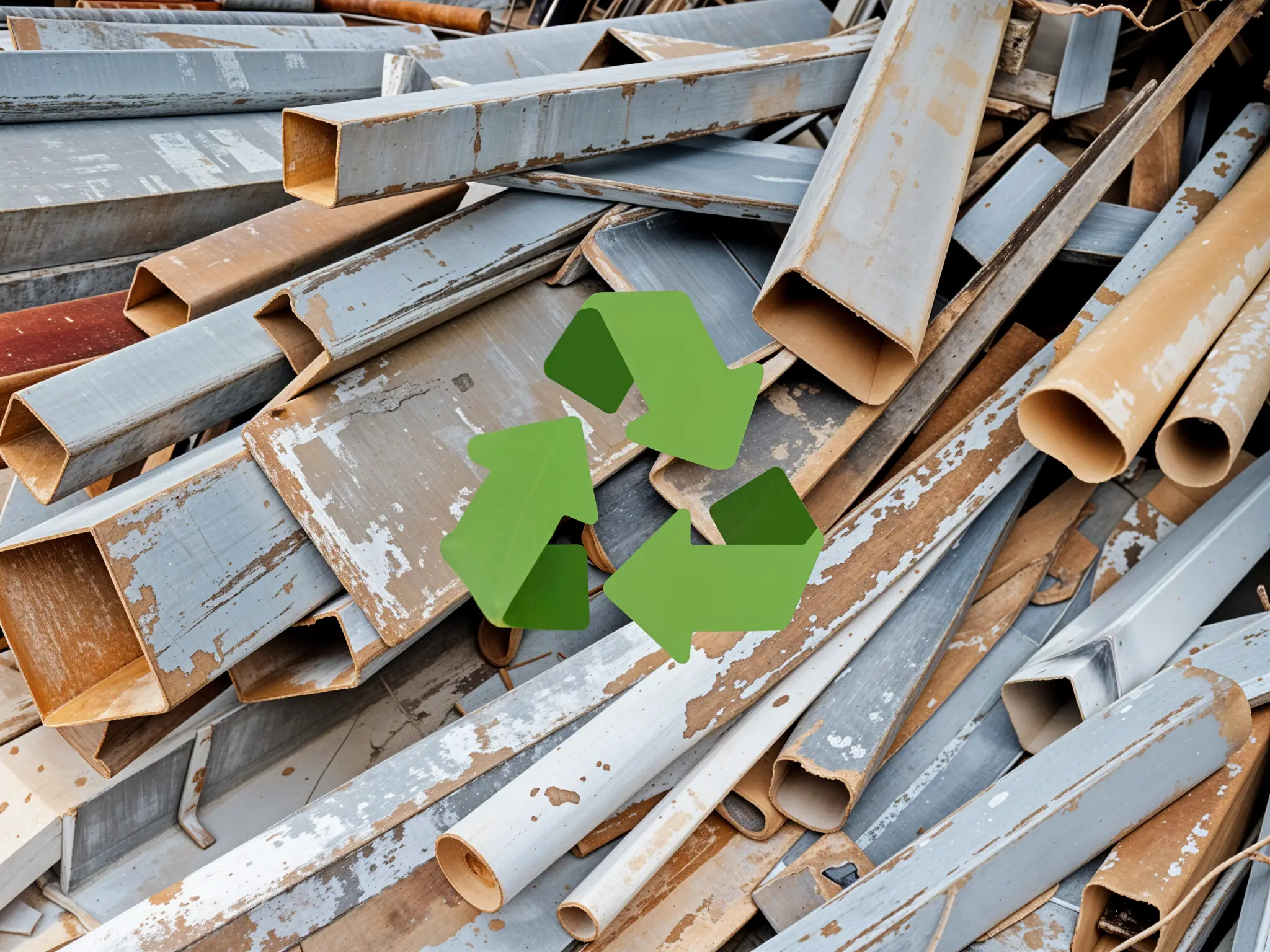
Another key player in environmentally friendly construction is recycled building materials like steel. This versatile material is transforming the industry by reducing waste, lowering carbon footprints, and contributing to the circular economy in construction. Recycled steel can be used indefinitely without losing its strength or quality, making it an attractive option for sustainable construction.
The environmental benefits of using recycled building materials like steel are significant. Recycling steel uses up to 75% less energy than producing new steel from raw materials. This reduction in energy consumption translates directly into lower greenhouse gas emissions, making recycled steel a much greener option.
In addition to its environmental advantages, recycled steel offers excellent mechanical properties. It provides a strong, durable alternative to wood, with the added benefit of being fire-resistant and termite-proof. In commercial buildings, recycled steel is used in everything from structural beams and columns to curtain walls and cladding.
Bamboo as a versatile construction material
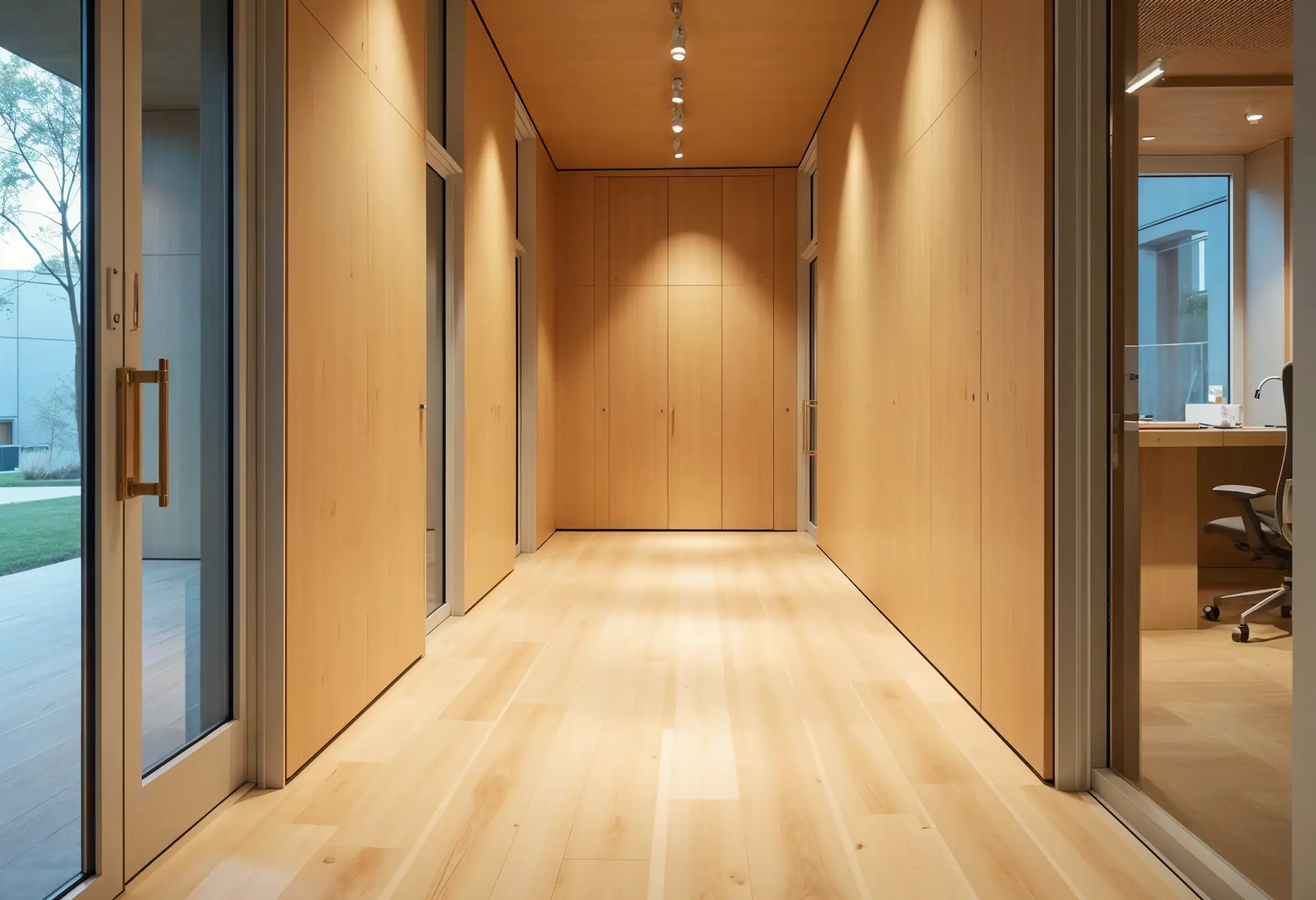
Bamboo construction material is emerging as a promising sustainable building material in Manhattan's construction scene. This fast-growing plant offers numerous advantages over traditional materials, making it an attractive option for eco-conscious builders looking for alternative building materials for low-cost housing.
Bamboo construction techniques like bamboo frames, bamboo panels, bamboo floors, bamboo foundations, and bamboo trusses showcase the material's strength and flexibility. Certain bamboo construction species have the compressive strength of concrete, making bamboo housing particularly resilient, even in the face of hurricanes and earthquakes.
Sustainable bamboo architecture is made possible through advancements like engineered bamboo, laminated bamboo, bamboo treatment, bamboo insulation, and bamboo jointing systems. These innovations enhance the durability of bamboo structures and enable the creation of low-cost bamboo house designs and prefab bamboo homes. By embracing bamboo housing, the construction industry is supporting environmental stewardship and utilizing rapidly-renewable materials.
To get a free consultation and quote on your next high-end renovation project using sustainable building materials, contact KS Renovation Group today.
Smart Technology Integration in Construction
The construction industry is embracing smart technology to enhance efficiency, safety, and project management. In Manhattan, these innovations are transforming how buildings are designed, constructed, and maintained.
IoT devices for real-time monitoring
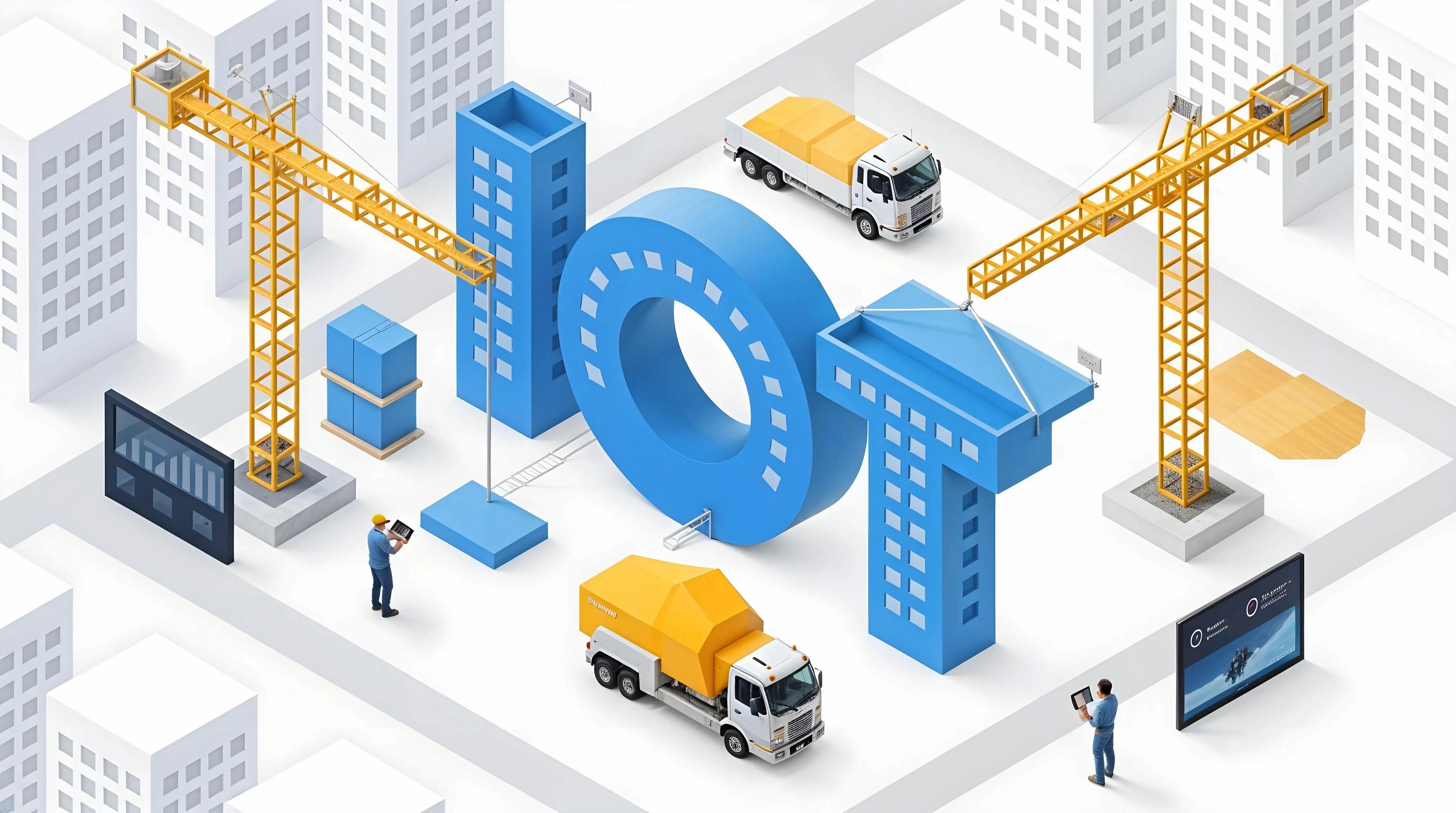
Internet of Things (IoT) devices are revolutionizing construction sites by providing real-time data and insights. These smart sensors and connected devices offer unprecedented visibility into various aspects of construction projects.
For example, IoT-enabled fuel sensors on construction sites help manage expenditures, refueling, and maintenance more effectively. This technology allows project managers to reduce costs and project duration significantly. Additionally, IoT-connected surveillance cameras and measurement sensors enable remote control and adjustment of machinery, increasing operational accuracy and efficiency.
One notable IoT solution making waves in the construction industry is Spot-r®. This technology uses sophisticated data capture and analytics to optimize resources, mitigate safety risks, and improve project management. Spot-r's wearable devices, affixed to workers' hard hats or bodies, instantly send alerts if a worker falls or is injured, addressing one of the most significant safety concerns in construction.
AI-powered project management tools
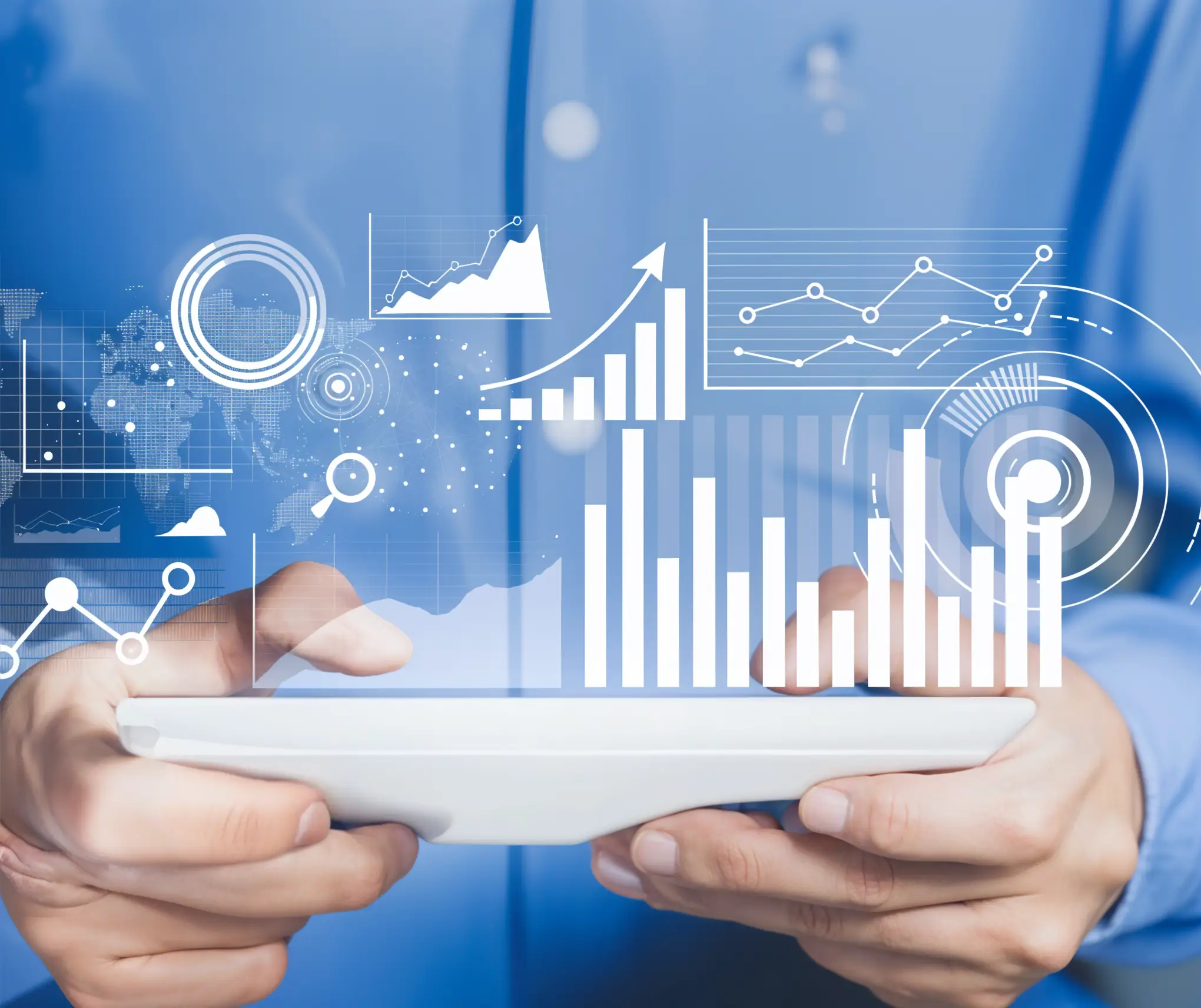
Artificial Intelligence (AI) is playing a crucial role in streamlining project management tasks. AI-powered tools analyze data to identify potential problems, such as material shortages or design flaws, earlier in the project lifecycle. This proactive approach helps construction companies avoid costly mistakes and meet project deadlines more consistently.
One example of an AI-powered tool making a difference is nPlan. This platform uses complex algorithms to map out the progress of vast infrastructure projects and avoid mistakes or supply gaps. nPlan's machine learning system was trained on a database of more than 740,000 projects, allowing it to forecast schedule outcomes using unbiased probability.
Another innovative solution is Buildots, which uses helmet-mounted cameras to capture footage of construction sites. The AI then analyzes this footage and compares it with actual designs to determine construction progress, providing a comprehensive view of project status.
Robotics in construction sites
The use of robotics in construction is rapidly developing, offering benefits such as increased efficiency, improved safety, and reduced costs. Autonomous construction vehicles, such as bulldozers and excavators, can be programmed to perform tasks like grading and digging without human operators.
Drones are also becoming increasingly common on construction sites. They're used for surveying and inspection tasks, reducing the need for workers to perform these duties in hazardous environments. This not only improves safety but also increases the speed and accuracy of data collection.
Collaborative robots, or "cobots," are another exciting development. These machines work alongside human workers, assisting with tasks such as lifting and moving heavy objects. This collaboration between humans and robots improves both safety and efficiency on construction sites.
To get a free consultation and quote on your next high-end renovation project using smart technology integration, contact KS Renovation Group today.
Modular and Prefabricated Construction Methods
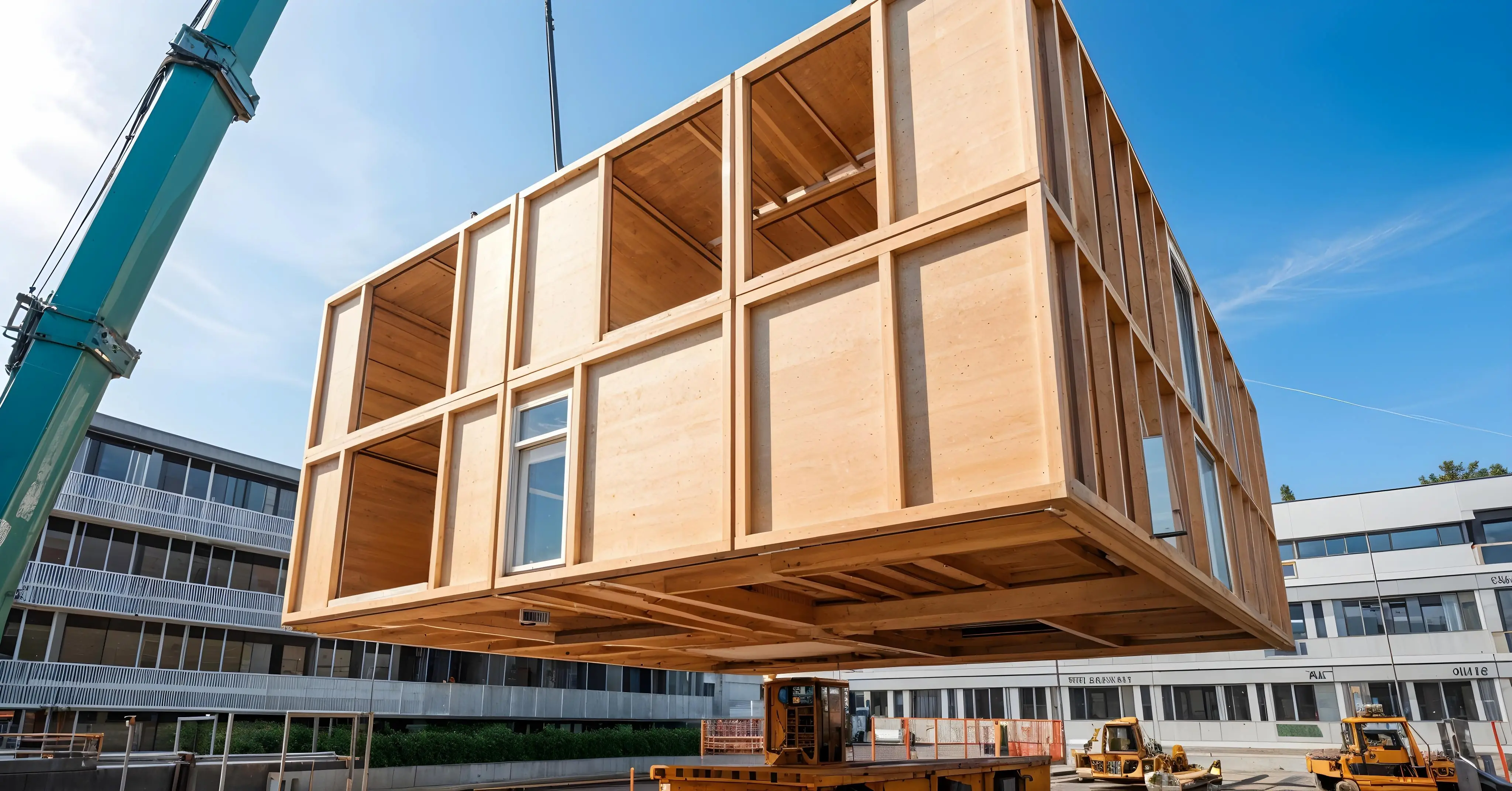
Modular and prefabricated construction methods are revolutionizing the building industry, offering innovative solutions to address the growing demand for efficient and sustainable construction technology. These methods involve designing, planning, and pre-fabricating different construction elements in a controlled factory setting before transporting them to the final location for assembly.
Benefits of off-site construction
Off-site construction provides numerous advantages over traditional on-site building methods. One of the most significant benefits is the increased efficiency and quality control achieved through lean manufacturing techniques. By utilizing Design for Manufacture and Assembly (DfMA) practices, modular construction ensures precise assembly tolerances and seamless integration of various building materials and features before installation on-site.
The controlled factory environment allows for better monitoring of each module or component, resulting in higher quality standards and more reliable outcomes. This approach also enables more accurate planning of budgets, materials, and labor, leading to decreased waste and cost savings.
Reducing construction time and costs
One of the primary reasons developers and constructors invest in prefabricated buildings is the significant time-saving benefits. Off-site projects enable teams to work in parallel tracks, with factory production and on-site preparation occurring simultaneously. This concurrent process can reduce construction time by up to 50%, making it an ideal solution for urban areas with urgent demands for residential and commercial spaces.
The streamlined production process in a factory setting is less affected by weather conditions, further reducing potential delays. This predictability ensures that projects stay on schedule and within budget. Additionally, the controlled environment minimizes material waste reduction in construction and maximizes recycling opportunities, contributing to overall cost reduction.
Customization options in modular building
Contrary to common misconceptions, modular construction offers remarkable design flexibility and customization options. Today's modular buildings support a wide range of architectural styles that seamlessly integrate with urban esthetics. Whether it's sleek high-rise apartments or innovative mixed-use complexes, modular construction allows architects to create visually appealing and structurally sound buildings.
The modular nature of these structures also enables easy expansion or reduction, adapting as the needs of the user change. This flexibility allows buildings to evolve with technological advancements or changing environmental standards, ensuring long-term sustainability and relevance.
As the construction industry continues to embrace modular and prefabricated methods, we can expect to see further innovations in design and customization options. The integration of technologies such as 3D printing, smart building materials, and advanced robotics is set to enhance modular construction capabilities, pushing the boundaries of what can be achieved in urban architecture.
To get a free consultation and quote on your next high-end renovation project using modular and prefabricated construction methods, contact KS Renovation Group today.
3D Printing Technology in Manhattan's Construction
3D printing technology is revolutionizing the construction industry in Manhattan, offering innovative solutions to address the growing demand for efficient and sustainable construction technology. This cutting-edge green construction technology is transforming how structures are designed, built, and customized, making it a significant construction materials trend for 2024 and beyond.
Large-scale 3D printed structures
Manhattan is embracing the potential of large-scale 3D printed structures to reshape its iconic skyline. This new concrete technology allows for the creation of entire buildings in a single, continuous process, significantly reducing construction time and costs. In fact, studies have shown that 3D printing can reduce construction time by up to 50% compared to traditional methods. This speed is particularly advantageous in urban areas like Manhattan, where minimizing disruption to the surrounding community is crucial.
One of the most exciting aspects of 3D printing in construction is its ability to create complex and unconventional shapes with ease. This opens up new possibilities for creative and sustainable construction, allowing architects and engineers to design structures that optimize natural light and ventilation, further enhancing energy efficiency in construction.
Reducing waste and labor costs
3D printing technology is making significant strides in reducing waste and labor costs in Manhattan's construction industry. The precision of 3D printers allows for exact material usage, minimizing waste and maximizing resource efficiency. In a case study of a 3D-printed building, it was found that construction managers had 30% to 60% less material waste compared to an average building of the same size.
Moreover, the technology has shown impressive cost-saving potential. By using 3D printing technology, investors have saved about 80% on labor and material costs. This substantial reduction in expenses makes 3D printing an attractive option for both large-scale projects and affordable housing initiatives in Manhattan.
Customized architectural designs
The flexibility of 3D printing enables architects in Manhattan to create highly customized designs that were previously difficult or impossible to achieve with traditional construction methods. The technology allows for the seamless integration of unique features, such as built-in green spaces or energy-efficient geometries, contributing to the development of more sustainable urban environments.
3D printing also facilitates the creation of lightweight structures without compromising strength and durability. This not only reduces the overall material requirement but also allows for the construction of more resilient buildings capable of withstanding environmental challenges, an important consideration for Manhattan's future urban development.
As Manhattan continues to evolve and face the challenges of urban growth and climate change, 3D printing technology is poised to play a crucial role in shaping the city's future. Its ability to minimize waste, optimize resource use, and enhance energy efficiency in construction aligns perfectly with the goals of eco-friendly building practices and sustainable construction.
To get a free consultation and quote on your next high-end renovation project using 3D printing technology, contact KS Renovation Group today.
Conclusion
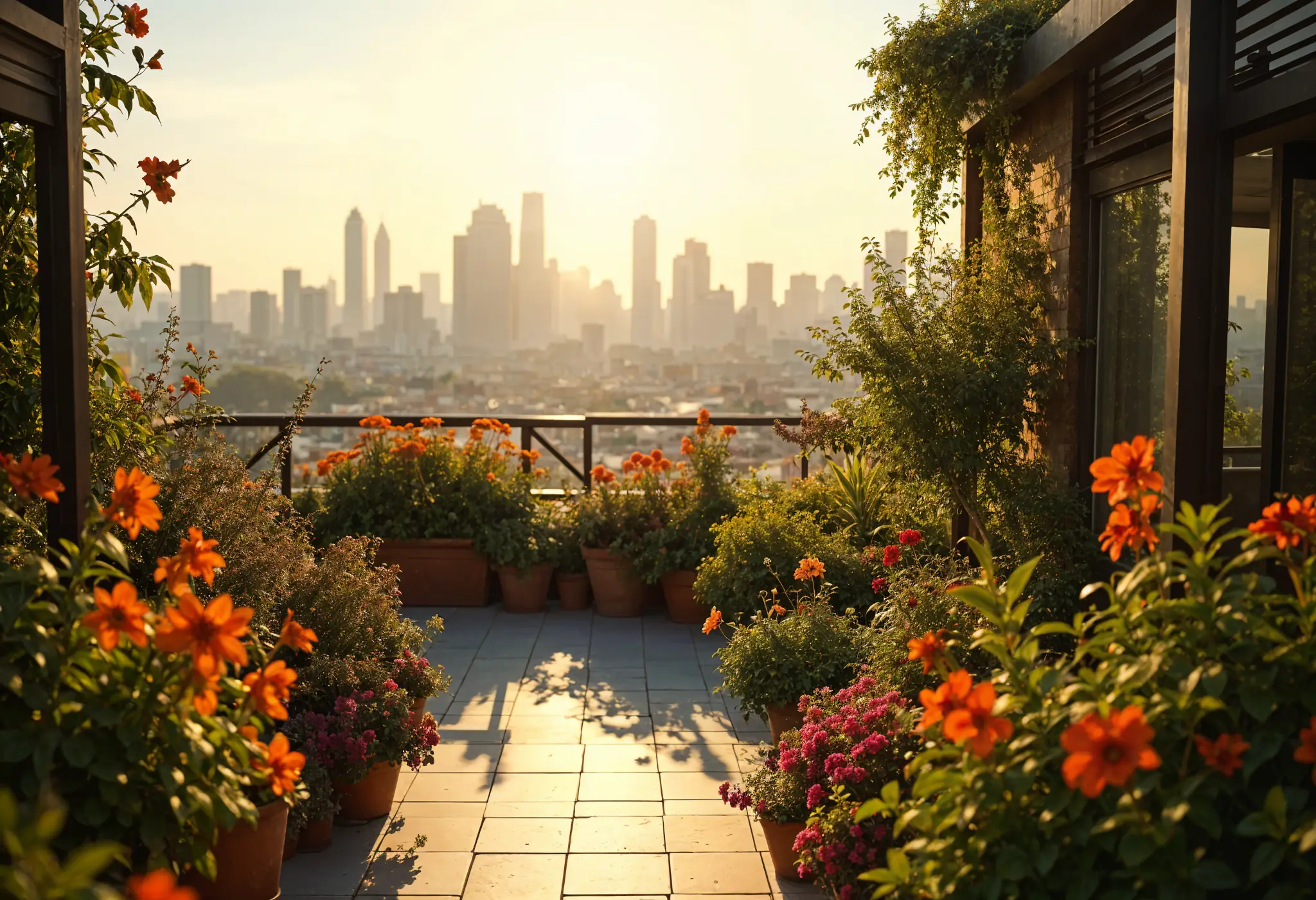
The construction industry in Manhattan is undergoing a remarkable transformation, with sustainable building materials, smart technology, modular methods, and 3D printing leading the charge. These innovations have a significant influence on how buildings are designed, constructed, and maintained, paving the way for a more efficient and eco-friendly urban landscape. The integration of these cutting-edge green construction technologies and materials is not just changing the skyline but also reshaping the very foundations of how we approach construction in one of the world's most iconic cities.
As we look ahead, it's clear that these trends will continue to shape Manhattan's construction scene in 2024 and beyond. The focus on sustainability, efficiency, and technological advancement is set to create buildings that are not only visually stunning but also more resilient and environmentally responsible. To explore how these innovative approaches can benefit your next project, reach out to KS Renovation Group for a free consultation and quote on your next high-end renovation project. By embracing these forward-thinking construction materials and technologies, Manhattan is building a future that's both impressive and sustainable.
FAQs
What are the key trends in the construction industry for 2024?
In 2024, the construction industry is emphasizing sustainability more than ever before. Companies are focusing on eco-friendly building practices, using sustainable building materials, and incorporating energy efficiency in construction to minimize their environmental impact.
How does the future of construction look in New York City for 2025?
By 2025, there is an expected decrease in new office construction by a million square feet annually. The focus in non-residential construction will likely shift towards manufacturing, educational facilities, and laboratory projects in New York City.
What are the top ten technologies and trends currently shaping the construction industry?
The construction industry is being transformed by several key technologies and trends, including digital software solutions, camera technology, augmented reality, building information modeling (BIM), drone usage, artificial intelligence (AI), robotics, and wearable sensors. These innovations are becoming integral, ranging from consumer applications to advanced medical solutions.
What is the next major innovation in construction technology?
The next significant advancements in construction involve the integration of Internet of Things (IoT) devices, drones, Building Information Modeling (BIM), augmented reality (AR), and virtual reality (VR). These technologies are revolutionizing project management by providing real-time data, enabling accurate project tracking, and enhancing safety on construction sites.
KS Renovation Blog
Get Inspired
Meaningful information about home remodeling for the true NYC homeowners.